Inside Rolex’s Swiss manufacturing facilities
After an intense three-day visit to Rolex’s manufacturing facilities, Carlos Pedroza is more convinced than ever of the luxury brand’s impressive quality and commitment to values and heritage
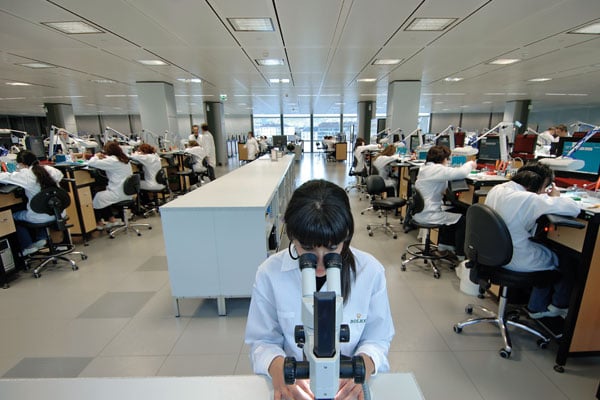
Generally, people think of American mass market brands as the pinnacle of successful global positioning. I may disagree.
There is one brand from Switzerland that is embedded into our childhood, into our very early memories. It is the remembrance of our first encounter with luxury: Rolex.
If you think carefully, you’ll find Rolex references on some of the most iconic films in history, as early as 1964’s A Shot in the Dark, and on several films with celebrity actors like Dustin Hoffman, Marlon Brando, Paul Newman or Faye Dunaway.
In sports, since 1978, Rolex has been the background of every single match played at Wimbledon, including the famous Björn vs McEnroe final in 1980. Rolex has been patron of the arts, horse riding, golf and several cultural expressions on a global scale. For the X, Y and Z generations, Rolex is part of the cultural landscape, not only as a luxury brand but as a reference of elegance, quality and professionalism.
A Rolex watch is also a status symbol; one that reflects a success story and has been embraced by celebrities, politicians and the business community. It is the most recognisable watch brand in the world and one that has barely made any major changes to its family of models.
Read: Rolex watch with Dubai Ruler’s name to be auctioned for up to $160,000
The big question is: Why is Rolex so celebrated and well known? It is branding? Is it tradition? Or is something else?
I believe it is something else. People buy a watch because they think, or have heard that it has certain quality elements that makes it durable, trustworthy, reliable. Those elements will fulfill their aspirations of accomplishment. It may be so, but in Rolex case, perception is not the whole reality. A Rolex is made with extremely high-quality standards; so high that they keep the whole process a veiled secret in the industry. So high that they have developed and implemented technology usually fitted for aerospace industries rather than watchmaking. And most importantly, they are made with extreme care. They are made with love and pride.
We had the very rare opportunity to go inside their manufacture facilities in Switzerland. Here’s a brief recount of the enlightening experience.
ACACIAS
World headquarters and watch assembly
In the main corporate headquarters or Rolex, inaugurated in 1965 and heavily renovated between 2002-2006, the power of the brand is palpable. There’s a strong feeling that something very relevant happens inside. Besides the corporate offices, this facility in Geneva houses the design, research and development departments and two 10 floor production units (with four of those underground), where the final assembly of the watches and the Superlative Chronometer certification take place.
The final assembly is a complex and detailed process, with components coming from all different sites of the manufacture process. Fitting the hands on the dial, casing the movement, fitting the bracelet, aesthetic and control measures and the registration of a unique serial number for the movement and the case in a centralised database are part of the process on this facility.
The Superlative Chronometer certification is a unique process that the brand implemented on top of the traditional COSC certification that is the standard on the Swiss watch industry. The certification involves a series of in-house tests, with a proprietary methodology and special equipment on the fully finished and assembled watch. It measures precision, power reserve, waterproofness and self-winding. The precision standards double the minimum requirements of the COSC certification, taking every Rolex to a -2/+2 seconds per day accuracy.
The certification comes with a five-year guarantee, something that is unique to the industry, and proof of the reliability of Rolex production process.
During our visit to the headquarters, we had the privilege to admire some of the treasures of the museum collection while attending a presentation of the history of the brand. Several famous editions of Daytona’s – the first Deep Sea prototype – legendary watches from the early 20th century and more that would be the dream of every avid collector were in front of us.
Plan-les-Ouates
Case and bracelets
All Rolex manufactures are impressive and sophisticated, but perhaps the most surprising and unexpected is Plan-les-Ouates. The reason is that this facility represents the commitment of Rolex to their in-house production integration.
The metal that Rolex uses for its cases and bracelets is mostly done in house, where “done in house” truly means it. They have their own metal foundry inside Plan-les-Ouates. There are several players in the watch industry that work with proprietary alloys and experimental materials, but the general rule is to work with third-party providers to make them real. Rolex takes this whole relationship in-house.
In the foundry, Rolex develops their three 18ct gold alloys (yellow gold, white gold and Everose gold) and works the Oystersteel that is so unique of Rolex, with extremely high corrosion resistant properties. This steel is used in the aerospace industry. Besides the foundry, there ́s a whole metal forming process for the gold, steel and platinum cases and bracelets, with special equipment commissioned specifically for Rolex, that assures the quality and specifications that Rolex requires.
At the same facility, there ́s the Rolex Central Laboratory where all metals are tested and have several quality control processes. With an electron microscope, they can detect any imperfection on the metals. Usually a slight color distortion or uneven pattern signals metal contamination and is then labeled as non-fitted for a case or bracelet. Friction, ageing and resistance tests are also conducted on this laboratory.
One Oyster case requires 150 operations, form metal stamping to satin finishing. A Rolex bracelet needs at least 190 components and hundreds of operations. The whole process is a mix of high technology, micro mechanical precision and hand-made craftsmanship. Ancient art meets the future in a perfect and balanced mix of commitment to quality.
Ceramic art
Plan-les-Ouates is also where the Cerachrom development takes place. This special ceramic, unique to Rolex, is a patented material used on their bezels. It is extremely hard, and corrosion resistant. The process involves a base of zirconium dioxide or aluminum oxide powder, mixed with binding agents and colour pigments, then put inside a furnace for days at temperatures of over 1,600C. Then finishing with special diamond tip tools takes place. Since 2013, Rolex has been a pioneer in developing a patented single two colour ceramic bezel for its GMT-Master II model.
Automated stock
A truly impressive feature of the manufactures is their automated stock system that’s state-of-the-art. At Plan-les-Ouates it has 12,000 cubic meters of vaults with 60,000 storage compartments and a rail network of 1.5km that allows the transport of component trays to the workstations directly. The system makes 2,800 transports per hour. Every single component is uniquely identified and delivered to the precise area and the right time to ensure that the manufacturing process is constantly fluent and on time. With the production volume that Rolex has, this system is a true logistics masterpiece.
Chêne-Bourg
Dials and gem setting
This whole facility is focused on the dial production and gem setting procedures. In this building, technology merges with ancient hand crafted art. The dials can be made of brass, gold or platinum as a base and can have 18ct yellow, white or pink gold appliques, PVD, lacquering, mother of pearl, meteorite or semiprecious stones and electroplating (application of coloured thin metallic layers to the dial).
Brass is a flexible material that is easy to stamp, machine and decorate. Rolex uses 12 steps to remove excess material from the brass plate. Amongst them: electroplating, hardening, electrolysis. Also, they use electric current to ionise and create a fine binding layer with an additional material to achieve different colours and textures. For gem setting, the dial has to be in gold. All the hour markers, Rolex crown and indicators are polished by hand.
Once a dial is coloured and engraved, there is a printing transfer process with a silicon head tool. It’s kind of a dial spa treatment, and extremely soft application on the dial, with a perfect result. In essence, is a similar process to traditional lithography on fine arts.
The gems used by Rolex are of prime quality. The diamonds are all colourless, flawless, with no inclusions at 10x magnification. No other watch company uses this quality of diamonds with the exceptions of high-end jewelers. Besides diamonds, Rolex has rubies, sapphires and emeralds. It is very relevant that Rolex is part of the Kimberley process against conflict diamonds. All stones are certified and conflict free.
Bienne
The movement
The final part of the trip is where the heart of the Rolex watches is done. The Bienne facility is fully dedicated to movement development and the process is mostly done by hand. There are 2,000 employees working on this site, the current building it was inaugurated in 2012 and it has the automated stock system in place and works mostly with solar energy. Each Rolex movement has from 200 to 400 components. The ébauches are made of brass, finished in machines made to Rolex specific standards. There are 350 measurement points just for the mainplate. There are five robots taking care of the components.
Rolex developed its own very special hairspring, the Parachrom, patented in 2000. It can be 10 times more accurate than a conventional spring and it’s antimagnetic. To make it, it undergoes fusion process to reduce the diameter of the rod until it reaches 5m long and becomes a wire. The last process takes it to 0.1mm diameter and 3km long. The hairspring final shape is rectangular. After the final size is achieved, the wiring process starts, then coiling and anodization. This hairspring is used in 22 Rolex calibers.
All Rolex calibers require a skilled watchmaker and several quality control stages. The most complex caliber in the current collection is the 9001 from the Sky-Dweller, with an annual calendar and two time zone function. One of the most famous is the 4130 that powers the Daytona, the legendary chronograph form Rolex.
Rolex manufactures in house the main plate, bridges and the most strategic components like the escapement and balance wheel.
After the extensive Rolex experience that I had the privilege of being part of, one thing is certain: If you have a taste for watches, even if you ́re not a technical geek or an amateur collector, owning a Rolex is perhaps the most important step into becoming a proud watch owner.
A Rolex will never age, will never be dated, will never disappoint. It will certainly never lose value. Owning a Rolex is a rite of passage into serious watchmaking.
Rolex innovations
Rolex has made a huge number of important innovations over the years. Here is a list of some of the most notable..
Parachrom
Hairspring
Syloxi hairspring
Chronergy escapement
Paraflex shock absorbers
Saros annual calendar
Cerachrom bezel
Ring command bezel
Ringlock system case arquitecture
Chromalight
Oysterflex bracelet
Rolex glidelock diving extension
Easylink comfort extension
Quality process testing
There ́s an automated 33-hour quality testing process for each watch. The components stock is fully automated and every piece is delivered to a station to be tested. All results are also centralised into a database, individually identified and sent back to the Bienne facility for reviewing.
To measure precision, there ́s a 2D camera and a 3D camera that evaluate the precision reading of the hands from every possible angle, all linked to an atomic clock as a reference. The positions testing has two more steps than the COSC test, 15 hours on seven positions.
For the self- winding system, there’s an acoustic test with several microphones, similar to a stethoscope, that listens to the sound of the movement, self- winding system and oscillating mass, to assure that the whole movement is healthy.
For the waterproof testing, most of the equipment is made by Comex and there’s different standards for professional and non- professional models. There’s a thermal shock test as part of this process.