Navigating supply chain issues to deliver giga projects
Successful destination-scale project delivery hinges on a radical shift from traditional supply chain management to an integrated model emphasising transparency, quality control, and strategic partnerships
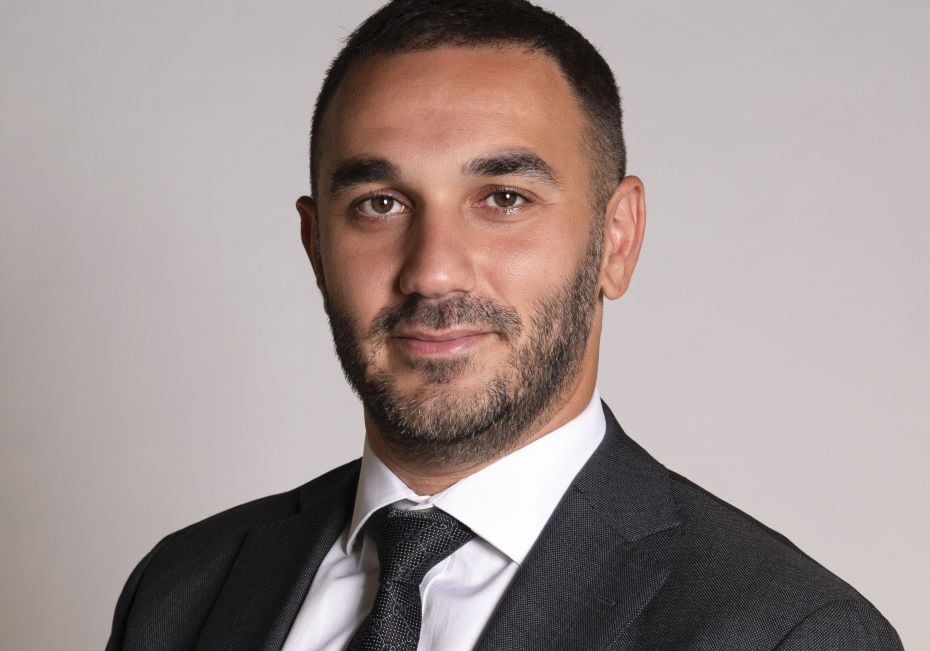
Building destination-scale projects is no easy feat. The complexity arises not just from the sheer magnitude of these developments but also from the multifaceted nature of navigating numerous stakeholders, materials, and processes to achieve a unified vision. Each stage, from the initial design to the final execution, is crucial in bringing these ambitious projects to fruition.
According to research by the University of Oxford, there’s a growing demand for these giga projects worldwide, which accounts for 8 per cent of global GDP. However, since the 2000s, only 0.2 per cent of these projects have successfully met their original cost and schedule estimates.
Delays in these projects are often the result of unforeseen global supply chain disruptions and insufficient oversight in material procurement, affecting their multi-year or even decade-long timelines. Consequently, systematic supply chain risk mitigation is a crucial area for asset owners to prioritise.
Doing so will enhance delivery efficiency, guarantee on-time completion, and successfully bring their visionary projects to fruition.
To achieve this, they must move beyond the traditional project management methods and adopt a more innovative approach that removes supply chain risk from the outset, guarantees certainty of outcome, and ensures sustained alignment with the project’s strategic goals throughout its duration.
Supply chain risk management and mitigation
Supply chain transparency is essential for the efficient management of destination-scale projects. Yet, traditionally, supply chains have not been designed with transparency in mind. Contractors and suppliers, often motivated by competitive advantages and fear of criticism, typically keep details of their upstream operations confidential.
This lack of openness poses significant challenges for asset owners, who already contend with numerous other concerns and possess limited capacity to thoroughly vet the multiple layers of suppliers and assess the quality of materials before they arrive on site.
This traditional project management model has several potential pitfalls, each posing considerable risks to asset owners, especially in ensuring timely project delivery.
A key factor determining the project delivery schedule is the procurement of building materials. This is because delays or inconsistencies in material supply can lead to significant project holdups, and the quality of materials directly impacts the overall project timeline and success. Indeed, an estimated 30 percent of global construction involves rework – essentially correcting mistakes attributable, in part, to sub-par materials and errors made during installation.
In the Gulf, these projects increasingly rely on a variety of traditional materials, such as natural stone, to reflect the region’s rich architectural identity and cultural heritage.
The inherent variability in these natural building materials adds an additional layer of complexity to the process, making it more challenging for asset owners to guarantee consistent quality and supply.
For example, when dealing with the high variability of natural stone, asset owners are faced with navigating a complex network of global suppliers, each providing materials of different qualities.
Managing a small quantity of such materials might be manageable. However, overseeing a supply large enough to cover the area of 100 football fields, a common scenario in destination-scale projects, is a far more daunting task.
Given these projects’ immense size and intricate supply chains, even minor quality issues can quickly escalate into substantial schedule delays if not identified and addressed promptly early on.
The complexity of this challenge is further amplified by the evolving landscape of environmental, social, and governance (ESG) regulations. As government policies grow stricter in many destination countries, asset owners find themselves increasingly accountable not only for their direct practices but also for their entire supply chain’s compliance with these standards.
For instance, the Saudi Stock Exchange has issued ESG guidelines, including metrics on material sourcing, supply-chain labour standards, and tax transparency.
Ignoring supply chain transparency can lead to potential regulatory violations, risking lawsuits, investigations, and even the withdrawal of investments, all of which can significantly hinder the progress of project delivery.
An innovative model for risk mitigation
All of these suggest that the traditional model of supply chain management for destination-scale projects is fundamentally broken and struggles to adapt to the dynamic realities of today’s environment.
To tackle these challenges effectively, asset owners must embrace a more innovative approach that bridges the gaps, ensuring transparency, quality control, and certainty of outcomes for project delivery.
What becomes essential for the asset owner in this context is finding a trusted partner who has both the capacity and expertise to manage and mitigate supply chain risks across the entire development life cycle, beginning from the design phase. This partner would function as an extension of the asset owner, employing their specialised knowledge and extensive experience in a specific industry to handle procurement processes effectively.
Consider the procurement of natural stone, for example. In this scenario, the specialist partner would utilise their unique industry expertise to aid the asset owner in selecting the appropriate stone and quarry to meet the asset owner’s vision, design, and budget constraints.
They would also evaluate potential suppliers on various parameters such as material quality, track records of past deliveries, and adherence to ESG standards.
Furthermore, they would offer actionable recommendations for optimising procurement strategies and oversee the on-site installation process.
Such partnerships not only ensure consistency and quality control throughout the project lifecycle but also bring the asset owner closer to the source of production, enhancing project delivery through timely and precise execution.
Within a wider scope, this integrated approach to removing supply chain risk holds promise for broader adoption across various sectors and industries supplying materials to destination-scale projects.
Implementing this strategy can enhance transparency across multiple supply chains, significantly improving the chances of on-time, on-budget project completion for asset owners.
The journey to successful destination-scale project delivery hinges on a radical shift from traditional supply chain management to an integrated model emphasising transparency, quality control, and strategic partnerships. This approach not only mitigates risk but also aligns closely with the evolving global landscape, offering a blueprint for future projects worldwide.
For asset owners, embracing this innovative model could mark a significant step towards realising their ambitious visions, ensuring these monumental projects are delivered on time and to their full potential.
The writer is the managing director of Versatile International.