From pit to port: Value chain optimisation is transforming mining
The advantages include reduced downtime, elimination of redundant operations, efficient energy consumption and ample room for innovations throughout the entire value chain
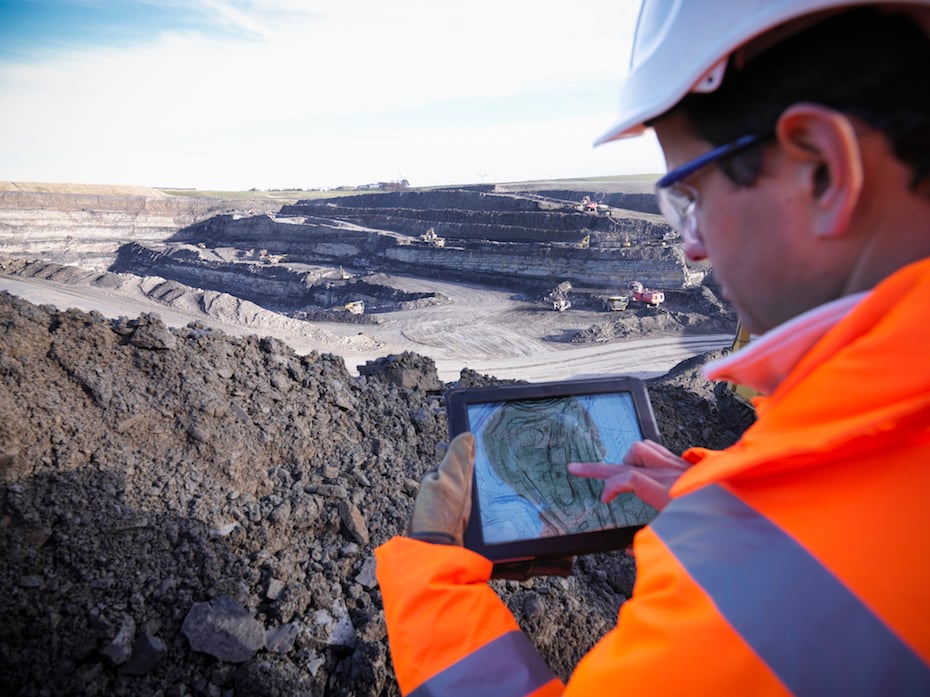
It is almost always bigger, bolder thinking that can improve how you work, as also protect the world you are working in. This is especially true in the mining industry, where organisations routinely struggle with uncertainty, productivity slumps, energy waste, high maintenance costs, suboptimal asset utilisation and slow decision making. The reasons for these constraints often boil down to one factor — poor visibility across the value chain.
No wonder mining operations are increasingly turning to digital transformation to connect and visualise the entire value chain. The advantages include increased throughout, reduced downtime, elimination of redundant operations, efficient energy consumption and ample room for innovations throughout the entire value chain — from the pit to the port.
Optimising for the new normal
Ramping up visibility also helps a mining organisation better adjust to the new normal, where many of its employees and decision makers are working remotely, or from home. Deloitte observes that while mining companies have been considering digital transformation for a while, the Covid-19 pandemic has truly accelerated its implementation. From responding, recovering, and ultimately thriving in the new normal, mining leaders have been presented with a great opportunity to avoid defaulting back to the traditional approach to work.
Instead, they can re-architect work, adapt the mining workplace culture and create a platform for innovation and collaboration using digital tools. Moreover, by bringing together data from on-field physical assets and enabling off-field remote and virtual access, “mining companies can improve their abilities to analyse real-time information; augment their digital capacities; and create platforms to integrate their data, analytics, and workflows”.
Towards a unified supply chain
Mining companies typically struggle from lost opportunities and gaps in understanding when using a menagerie of point solutions. To remain competitive, they need to regain operational visibility and maximise profits with a transformative approach to production and value chain optimisation. Deploying unified enterprise applications across the entire supply and demand chains ensures that every facet of the operation is now empowered with analytics and insights. This invariably transforms the organisation from being reactive to being predictive and allows it to drive operational excellence across the entire mining value chain.
A robust unified decision-making tool is the one that can deliver the means to cut losses along the value chain, enhance collaboration across silos, and decrease the total cost of ownership of various assets. The solution should be able to seamlessly bridge people, processes and technologies, while offering enhanced visibility across the whole value chain, from pit to port operations. It should eliminate the need to have specialists or application experts operating it.
Meets diverse needs
Perhaps the most important requirement from a unified supply chain tool is that it needs to be able to collect, store and enhance real-time operational data and enable cloud-based solutions, so that anyone in a mining organisation – no matter where they are located or whether they are working remotely from home – can access it. This also means collaboration across team becomes easy. Other qualities in a well-rounded tool include the ability to integrate the mining organisations plans with an ERP and geological modeling system. This ensures the organisation can be proactive, agile, and responsive during the planning and scheduling stage itself. It also fuses contractual constraints with operational constraints. Besides, by modeling the entire supply chain in a single space, the organisation can see all hardware and software constraints in the context of its supply chain, and thereby optimise various KPIs.
Finally, the unified supply chain solution should be able to cater to the mining company’s evolving needs – which can change rapidly, especially in this post-pandemic world. It should come with multiple hosting options and be able to scale up or down to always be in sync with current business priorities.
Connections from pit to port
Australia’s iron ore mining project, Roy Hill, wanted to build a greenfield mine process plant based on modern control room automation principles. It also wanted to establish end-to-end visibility of the entire mining value chain. Their key challenges included eliminating organisational silos, realising resource-to-market potential by avoiding hidden inefficiencies, and being able to connect, automate, and control each component of the pit-to-port mining site from a control center located 1,300 km away from operations.
Aveva worked closely with Roy Hill to establish a remote operations centre that centralised all roles and functions linking mining operations. It created a fully integrated, greenfield mine-to-port operation that is controlled remotely, while streamlining processes by facilitating collaboration among different functions, and creating a high-performance team connected by a digitised process.
May the force be with your mine
World Economic Forum points out that within the mining and metals industry, digitalisation will be the force that changes the nature of companies and their interaction with employees, communities, government and the environment at every step of the value chain. “From mineral exploration and valuation, through mining, ore processing and metals production, to downstream sales and distribution, digitalisation is blurring traditional industry lines and challenging the business models of the past.”
In short, optimising the entire value chain will not only open the path to more profits, but also to a better future.
Martin Provencher is the industry principal, mining, metals and materials, Aveva