Why capturing and recycling sulphur dioxide is so crucial
Along with reducing fossil fuels such as carbon dioxide and methane, capturing and recycling sulphur dioxide is crucial for reducing environmental damage

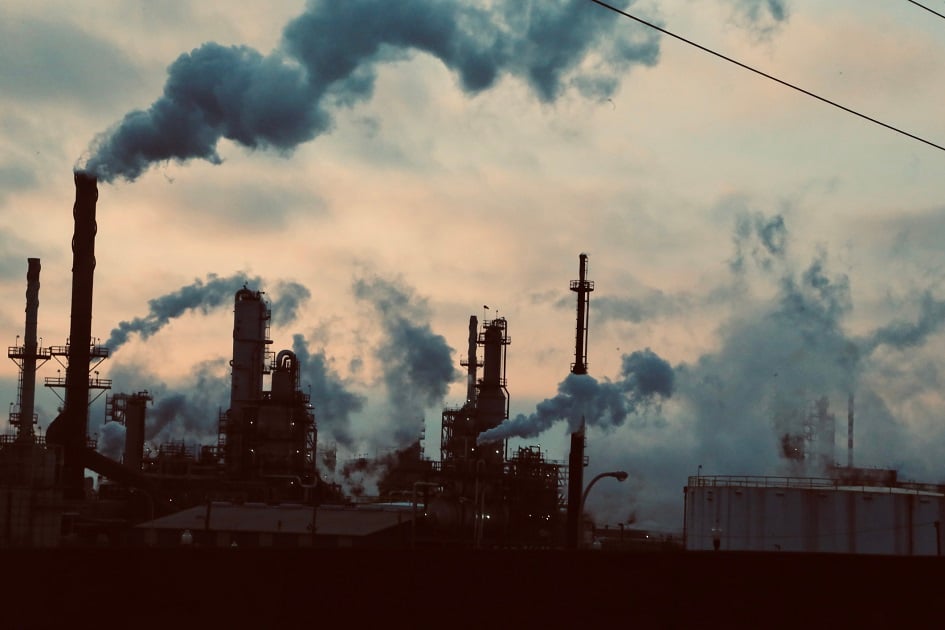
In the face of increasing environmental concerns, key industrial sectors such as base metal smelters and coal-fired power plants are intensifying efforts to curb sulphur dioxide (SO₂) emissions. These industries, traditionally significant contributors to atmospheric SO₂, are now actively remodelling their facilities with effective emission-reducing technologies.
This article explores the origins of sulphur dioxide emissions, their impact on the environment, and the current strategies industries are employing to minimise their ecological footprint.
Sulphur dioxide (SO₂) is a colourless gas with significant environmental impacts at high concentrations. It forms sulfuric acid when reacting with atmospheric moisture, leading to acid rain. Major natural sources of SO₂ include volcanic activity, but significant industrial emissions arise from smelting base metals like copper and nickel and burning sulphur-rich fossil fuels.
South Africa’s power utility, Eskom, ranks as the world’s largest SO₂ emitter, surpassing the entire energy sectors of some countries, including the United States and China. Non-ferrous metal production is another major source. For example, the Southern Copper Corporation’s smelter in Ilo, Peru, emitted substantial SO₂ from processing high-sulphur (33 per cent) copper concentrate before modernisation.
Capturing and recycling sulphur dioxide is crucial for reducing environmental damage. One common method is converting SO₂ into sulfuric acid, although this process involves challenges in storage and transport, as well as the need for clean raw emissions to ensure the acid’s usability.
In the 1990s, Rio Tinto modernised a Utah-based copper smelter to produce sulfuric acid, thereby reducing SO₂ emissions. Over 20 years, the company invested $5 billion, leading to a sulphur recovery rate of 99.93 per cent and making the plant one of North America’s largest sulfuric acid producers.
A similar initiative by Southern Copper Corporation in Peru improved its SO₂ capture rate from 33 per cent to over 92 per cent with a $600 million investment.
In a more recent push for lower sulphur impact, Russia’s top metals producer Nornickel has addressed SO₂ emissions by launching a Sulphur Programme at its Arctic factory, the Nadezhda Smelter. This project aims to convert SO₂ into sulfuric acid and gypsum, with an estimated capture of 1.5-1.7 million tons of SO₂ annually. The initial investment at the Nadezhda Plant is around $2 billion, aiming to reduce SO₂ emissions by 45 per cent in the Norilsk Division.

Despite their high costs, these initiatives underscore the industrial commitment to minimising environmental impact. While they may not yield immediate financial returns, they are crucial for long-term environmental sustainability and public health.