Aircraft Interiors: The Future Is Lighter
Carrier demands for better fuel efficiency is rewiring aircraft interiors, writes Kim Choate, director of Mass Transportation for SABIC’s Innovative Plastics business.
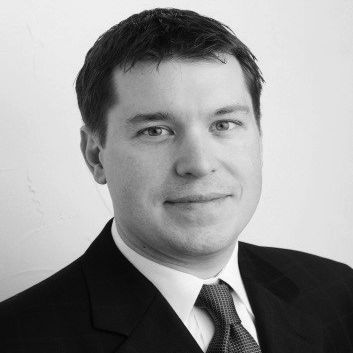
Driven by rising income levels and the development of specialised tourism centres, such as medical hubs in the UAE and religious centres in Saudi Arabia, the Middle East is expected to experience faster growth in passenger air travel than any other region of the world between 2012 and 2032, according to a report from a GCC-based financial analysis firm Alpen Capital.
This represents both a challenge and an opportunity to airlines in the region.
To attract consumers, airlines must enhance the on-board passenger experience, maintaining a strong interior branded look and feel to differentiate themselves from competitors, and they also need to improve fuel economy if they are to maintain their competitive advantage and operate in a sustainable way.
Lightweight solutions to support aircraft interior design, such as high- performance engineering thermoplastics, are transforming the industry by enabling manufacturers to create components that are significantly lighter than those made from traditional materials such as metal, but also offer greater design flexibility.
While metals and polyvinyl chloride- (PVC) based materials are traditionally used today, the aviation industry will now also have to look at the potential of high performance engineering thermoplastics, such as polycarbonate and polyetherimide.
On an average, an aircraft will burn about 0.03kg of fuel per hour for each kilogramme carried on board. Given that the total commercial fleet flies approximately 57 million hours per year, cutting just 1kg per flight would save roughly 1,700 tonnes of fuel and 5,400 tonnes of carbon dioxide per year, according to commercial aviation industry body Air Transport Action Group’s Enviro.aero initiative.
Using a lightweight solution to replace aluminium in a tray table arm can offer significant weight reductions of up to 40 per cent while also providing comparable strength. Even when compared to other plastics currently available, polycarbonate can make an impact.
For example, using extremely light thermoplastic sheet options available today to replace polyvinyl chloride and acrylic blend (PVC/ PMMA) products on seat tray table shells can help reduce weight by approximately 121.6kg based on an aircraft with an average of 190 seats. This can help the total commercial fleet save roughly 206,720 tonnes of fuel and 656,640 tonnes of carbon dioxide per year.
Helping to reduce fuel consumption is only one aspect of how today’s lightweight solutions are changing the industry.
For example, designers are often restricted by the clarity and compliance limitations of the transparent materials currently available to them.
In early 2014, a transparent polycarbonate material was launched that offers the highest light transmission of any OSU (Ohio State University)-compliant sheet available today. This type of sheet allows manufacturers to design large transparent components such as security partitions and oversized windows, which are becoming increasingly popular in top deck designs.
Additionally, it enables future innovation, helping designers find solutions to currently unmet needs, such as the evolution of self-service refreshment stations on aircrafts, which require large transparent windows so passengers can see what is available.
The benefits of today’s lightweight solutions are myriad: whether it’s enhancing fuel economy or offering design flexibility. As passengers demand more from airlines and aircraft, the industry will have to look at lightweight materials to answer these challenges.