The power of four: digitisation, automation, sustainability and data
Craig Hayman, CEO, AVEVA provides technological predictions for the industrial sector in 2021
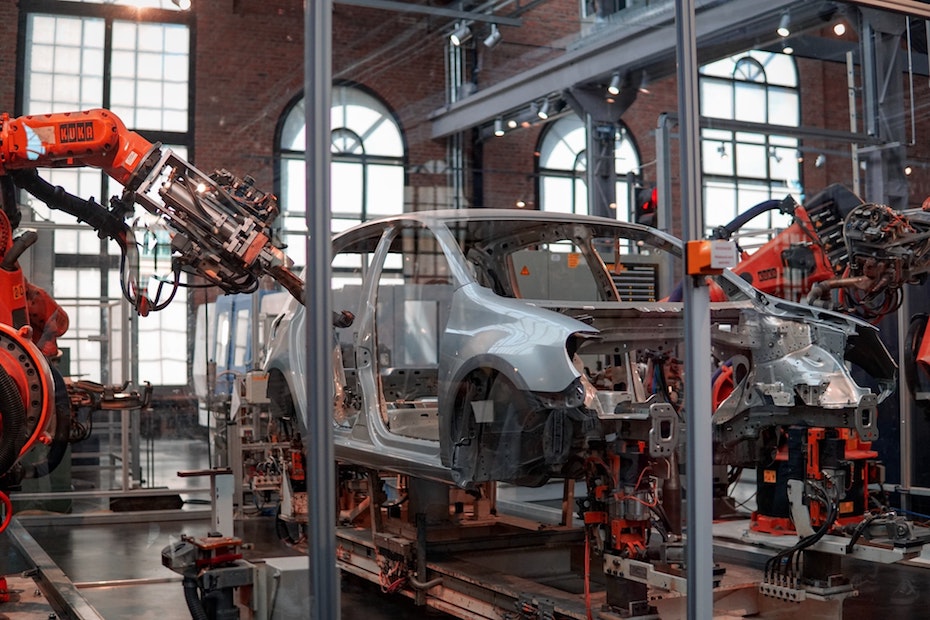
Technology has become deeply embedded in almost every facet of modern-day life and plays an intrinsic role for many businesses across the globe. Digital transformation is enabling organisations, particularly in the industrial sector, to enhance their capabilities, and increase their returns across their assets and operations. The use of the industrial internet of things (IIoT) through real-time analytics has had a profound impact, by improving response times to potential issues and minimising possible damage to the environment, which has resulted in the avoidance of costly unscheduled shutdowns, while improving profits.
As we look ahead into 2021, four key technology predictions stand out for the Industrial sector. First, digitisation will continue to spread and mature within organisations – connected IIoT will go deeper and wider across the core of many businesses. Second, artificial intelligence (AI) and machine learning (ML) enabled technologies will continue to automate processes to deliver improved performance and agility. Third, there will be greater focus on sustainability as businesses look to become cleaner and more efficient in their use of natural resources. Fourth and not least, businesses will look to unlock critical insights from data.
Digitisation will deepen and cloud usage will mature
Digital capabilities strengthen resiliency. 2021 will pave the way for further digital transformation within industrial sector organisations. Across industries, business leaders are also turning to technologies such as AI and 3D modelling to understand their production processes and plans. To adjust to an environment where the supply of raw materials is volatile and demand for end products is focussed on the essentials, businesses must understand their production facilities better than ever before.
Cloud is not necessarily a pre-requisite for digital transformation, but an enabler. Cloud technology accelerates time to value, increases collaboration, and reduces costs. What’s been evident in 2020 is that a cloud platform allows organisations to consolidate data from multiple sources into a central location for improved transparency and accessibility – at any time, any place and from any secure device.
The current crisis is accelerating the use of cloud and data in increasingly sophisticated ways to help provide visibility and certainty into operations. The adoption of analytics is said to be one of the greatest drivers of digital transformation, as businesses seek greater data-driven insights. Data acts as a source of truth that aids teams to focus on the critical factors that determine business resilience. There has also been a fundamental shift in mindset: customers now understand where they need to get to and how quickly they need to get there. In an age where time is progressively of the essence, an increased focus on digital transformation and data-driven insights will be a game changer.
Automation will pick up pace
According to Gartner, “By the end of 2024, 75 per cent of enterprises will shift from piloting to operationalising AI, driving a 5x increase in streaming data and analytics infrastructures.” Boosting augmented data management systems with AI, will also help to optimise and improve operations. Examining large samples of operational and historic data will become the norm.
We will also see AI applications increasingly being supported by devices and sensors connected through the IIoT. The combination of IIoT and AI has begun the next wave of performance improvements, especially in the industrial sector. Furthering this automation, AI uses the historical IoT data to analyse trends which can help in streamlining and improving the supply chain process through cutting-edge solutions such as AI-driven operations scheduling. This provides recommendations to humans as to the optimal scheduling sequence, substantially reducing error and inefficiencies.
Sustainability will be embedded within businesses
Sustainability is a journey beginning by measuring where organisations are. Digitisation is the natural first step for a fact-based approach. This data allows complex businesses to develop a meaningful strategy and execute it on the ground.
Industry 4.0 will help to bring information together to build a digital twin that allows organisations to optimise sustainable processes. If we take the energy sector, in the past few months jet fuel consumption dropped dramatically, however energy consumption overall remained relatively stable, and electricity demand grew. Electricity remains the most efficient way to distribute energy around the world. In manufacturing in comparison, many companies’ supply chains could not flex at the same pace as the world was changing. Moving forward, these companies will pivot to use local suppliers to meet specialist requirements and with lower emissions.
The industrial development is crucial for economic growth, eradicating poverty and employment creation. However, increasing resource-use efficiency and enhancing technological innovation offers real opportunities to reduce costs, increase competitiveness and employment. The industrial sector, although late to the digital transformation process, has a unique opportunity to lead the way in making a significant impact to the planet.
Data repositories will acquire memory
The adoption of data analytics is said to be one of the greatest drivers of digital transformation, as businesses seek greater data-driven insights. Data acts as a source of truth that helps teams focus on the critical factors that determine business resilience. Businesses are acutely aware that they must become more resilient by using technology.
Companies are using IIoT to their advantage to securely connect, and collect data from diverse remote assets, channeling information to advanced operational applications, and closing the loop by feeding key business applications. This helps to enable optimisation, asset management, enhanced analytics, and modelling/simulation – and this ultimately means improvements in business efficiency across the entire operations.
This has been particularly true for the industrial sector, where data has had a significant impact in five key areas:
• Real-time operational information is increasingly being used to understand what is happening in real-time and enables the condition management of asset and operations lifecycles. For example, a dashboard displaying the vibration frequency of a rotating asset such as a turbine during operation provides real-time understanding of the asset operational behavior and state.
• Historical operational information helps organisations to understand what has happened in the past to create intelligence around operational behavior of assets. Through operational trends, display of KPIs and dashboards, you can create abstracted views of operational states. For example, a graph may be displayed on a dashboard showing the turbine’s past vibration frequency during operation. This can be compared to the real-time vibration frequency, creating intelligence on the asset’s long-term operational trends.
• Predictive analytics is used for what-if type modeling. Integrating real-time and historical data enables your team to assess potential outcomes of operational states and behaviors, even accounting for tertiary variables. Deterministic or non-deterministic models can then be applied for open-loop simulation and predictive analytics. For example, you can now estimate how long a piece of equipment can run before it requires inspection or is predicted to fail.
• Prescriptive analytics describes what’s needed to optimise asset and operations lifecycles. Scenario-based guidance is created and delivered through learning elements and closed-loop algorithms to enable your team to calibrate planning and scheduling across the entire enterprise value chain. For example, using a unified supply chain model, scenario-based calculations can be used to optimise maintenance schedules and performance, minimising impact to your operations.
• Enhanced safety is achieved through a combination of connected IoT devices, augmented and virtual reality technology, which provide real-time operating procedures and key messages to operations personnel, reducing human error for performing specific tasks.
Be bold, reflect and evolve
Uncertainty is here to stay, as well as the possibility of a resurgence of Covid-19, the length and depth of the economic downturn, trade wars, oil price fluctuations and so forth, so businesses must take lessons learned from uncertainty and create their new normal.
What lessons have we learned from 2020? Businesses require intelligent software to address industrial pain points for value creation, productivity improvement, insight discovery, risk management, and cost optimisation. With the right technology, businesses can be incredibly agile to manage costs, boost efficiency and avoid costly mistakes. The combination of digitisation, automation and data driven insights, with a focus on sustainable business can be a key differentiator and a propelling force to help ensure businesses meet their goals of today and tomorrow.